
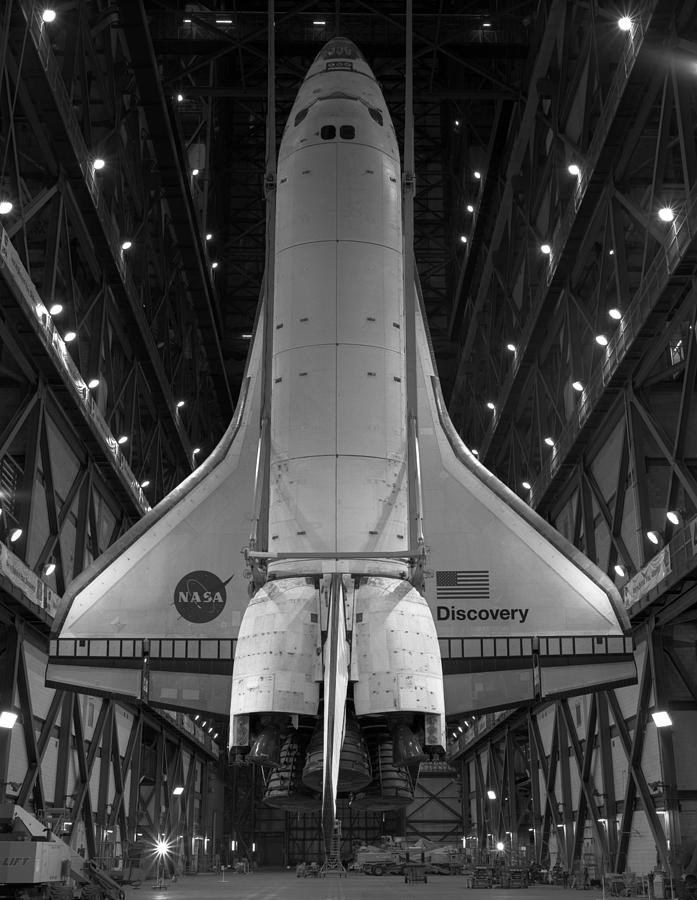
"They had not developed what's called the densification process for the tiles yet," said Barnes. Mark Barnes, a USA orbiter operations manager, also worked at Kennedy when Columbia arrived from its assembly plant in Palmdale, Calif., and remembers one of his first jobs in shuttle processing. "It keeps everyone in a competitive spirit and keeps everybody on their toes." "We all think we're the best, which is good," Bingham said. "They set the tone for their team much like a commander sets a tone for a mission." "We do virtually the same testing and checkout and work on the three orbiters, but each team has its own feel and it's really created at the leadership of the team from the flow director on the NASA side and the flow manager on the USA side," said Shuttle Launch Director Mike Leinbach. Next, it's on to about three month's worth of work to check the heat shield tiles, swap out the space shuttle main engines, or SSMEs, and assess the vehicle's structural, mechanical and electrical integrity.Īll of that painstakingly detailed work requires quite the team effort. Then, they remove the previous mission's payload. Photo credit: NASA/Jack Pfallerīingham began working at Kennedy in the late 1970s to prepare shuttle Columbia for its first flight, STS-1, and said the day-to-day operations in an OPF are like working in a garage.ĭuring the first couple of days after a shuttle returns from a spaceflight, technicians remove hazardous chemicals like fuel, dry the engines and open the door panels to gain access. Image: Workers watch as shuttle Atlantis slowly backs out of OPF-1 during its rollover to the Vehicle Assembly Building for its final mission, STS-135. Inside the OPF, Discovery will be prepared for future public display. Image: Shuttle Discovery's tail fin clears the hangar door of Orbiter Processing Facility-2 at the end of its 39th and final spaceflight mission, STS-133 in March 2011.
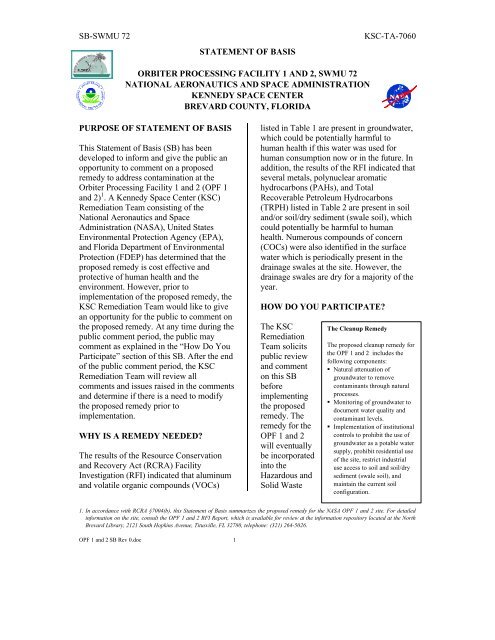
Image: In OPF-2, technicians check out space shuttle Endeavour's payload bay before its final mission, STS-134. Image: In September 1983, technicians in Orbiter Processing Facility-2 inspect Spacelab-1 in the payload bay of shuttle Columbia. Columbia then was towed into an OPF for processing for STS-1, NASA's first shuttle fight. Image: Shuttle Columbia arrived at Kennedy's Shuttle Landing Facility via the shuttle carrier aircraft in March 1979 after completing its ferry flight from Dryden Flight Research Center in California. "We try to keep the platforms within a maximum distance of 6 to 8 inches, but a minimum of 4 inches." "Each high bay has a footprint of the orbiter, and when it rolls in, it has to fit to that footprint," said Wayne Bingham, a United Space Alliance, or USA, flow manager. Once inside, technicians jack-and-level the shuttle to maintenance height where platforms and a main access bridge surround the spacecraft like a glove. Across the street is OPF-3, the home base of Discovery. In recent years, OPF-1 and OPF-2, which are connected by a 233-foot-long low bay, have been the residence of Atlantis and Endeavour, respectively. But it's also a place where staples are prohibited from the paperwork technicians work off of so the little pieces of metal don't accidentally become embedded in the shuttle's critical systems.įresh off Kennedy's Shuttle Landing Facility and back from a mission, shuttles are towed to their individual processing bays.

The bays may be the highest-tech garages on the planet, where workers ready a spaceship for flight without scuffing it and huge cranes move tons of cargo into place. They're formally called orbiter processing facilities, but routinely go by the names OPFs, bays, or hangars, and inside highly experienced technicians perform two-thirds of the work to prepare a shuttle for space. If home is where the heart is, then the heart and soul of NASA's space shuttle fleet reside in three custom-built, 29,000-square-foot buildings at Kennedy Space Center in Florida.
